Electric motors are vital components in various industries, yet they endure wear and tear over time. If you notice reduced motor efficiency, it’s a sign of deterioration. Two options emerge when faced with motor failure or impending breakdown: motor replacement or rewinding. A thorough motor diagnosis by an expert, like electric motor rewinding by Al Ghaima, is crucial before making a decision. While motor replacement is conventional, motor rewinding, an armature winding process restoring motor efficiency, offers compelling reasons to consider.
Eco-Friendly Solution
Electric motors consume substantial energy, contributing to high operational costs. Purchasing a new engine incurs significant expenses and a larger carbon footprint due to production. In contrast, motor rewinding recycles most old motor parts, significantly reducing environmental impact. Although demanding expertise, modern techniques have improved effectiveness, making rewound motors eco-conscious and cost-effective.
Cost-Effective Approach
Motor rewinding costs around 40% of a new motor, appealing to budget-conscious businesses, from small engines to 100+ horsepower giants. However, not all motors suit rewinding. If laminations or the magnetic core are damaged, rewinding may not work. The same applies to engines with bearing failures. Yet, rewinding proves a sensible and cost-efficient choice when the magnetic core remains undamaged.
Enhanced Efficiency
Contrary to the misconception that motor rewinding reduces efficiency, modern techniques often enhance motor performance. Old and damaged coils may be replaced with new ones during rewinding, ensuring the motor operates within precise tolerances. This meticulous approach improves, rather than diminishes, motor efficiency.
Partnering with Motor Rewinding Experts
Renowned Electric has collaborated with diverse industries for three decades to reduce electric motor rebuilding and rewinding costs while maximizing machine efficiency. Our team of motor rewinding experts possesses the required skills and experience, ensuring high-quality work with swift turnaround times.
Understanding the Value of Motor Rewinding
Electric motors represent a significant capital investment, and their annual operational costs can far exceed their purchase price. Efficiency is a top concern for plant operators. While it’s commonly believed that motor rewinding results in efficiency loss, this notion needs to be updated.
The Value of Motor Rewinding
A Green Motor Practices Group study reveals that properly executed rewinds do not compromise electric motor efficiency. Advancements in materials and craftsmanship play a pivotal role in achieving this outcome. Better resins and insulating tapes enhance thermal dissipation, while automated coil-forming technology ensures consistent coil duplication for improved performance.
A qualified service provider can guarantee that the rewound motor meets or exceeds the original OEM efficiency. The process should begin with a comprehensive assessment, including recording nameplate data, a visual inspection, and winding details.
Core Integrity Matters
Core integrity is fundamental to motor efficiency and reliability. Damage to the core is among the first issues a reputable service provider will check visually and through testing. Extreme care is taken during the repair process to maintain the quality of the steel lamination core plate.
On Premium Efficient motors up to 300 hp (NEMA sizes), core damage may render repair unfeasible, making motor replacement more economical. However, repairs and rewinds on larger machines can offer excellent value, cost-efficiency, and return on investment. Cores can be repaired by replacing damaged laminations with equivalent components, ensuring the core returns to its original dimensions.
Enhanced Winding
Improvements in winding provide significant opportunities to enhance motor efficiency. The service provider can increase wire diameter, optimize copper packing in slots, and reduce the length of coil loops, boosting power density and efficiency.
Premium Efficient motors, designed to run cooler and use high-grade materials, offer greater efficiency, while oversized motors, a common practice for enhanced reliability, tend to be costlier to operate without necessarily extending service life.
Efficiency and Loading
Motors operate most efficiently when fully loaded. Oversized motors, although intended for reliability, often lead to inefficiency. Premium Efficient motors are designed for improved efficiency, reduced operational costs, and a better return on investment.
Conclusion
Motor rewinding, often misunderstood, emerges as a practical and eco-conscious choice. It preserves efficiency, reduces costs, and minimizes environmental impact. When handled by qualified experts, motor rewinding can match or exceed the performance of new motors, ensuring reliable and efficient operations. Partner with experienced service providers like www.ghaimagroup.com to unlock the full potential of motor rewinding and make informed choices for your business.
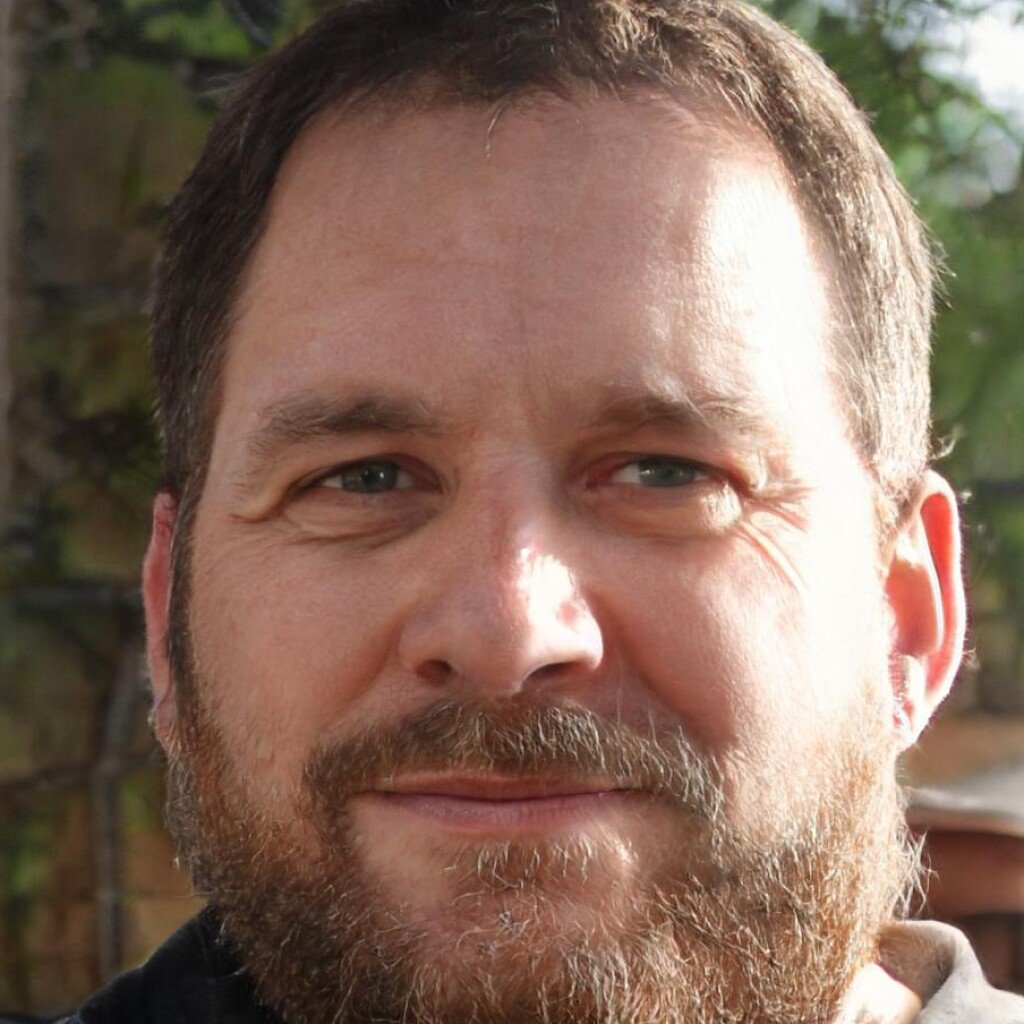
Soccer lover, tattoo addict, music blogger, Bauhaus fan and fullstack designer. Operating at the crossroads of design and intellectual purity to save the world from bad design. Check me out on Dribbble or Medium.